فرآیندهای حرارتی بر روی ورق استیل
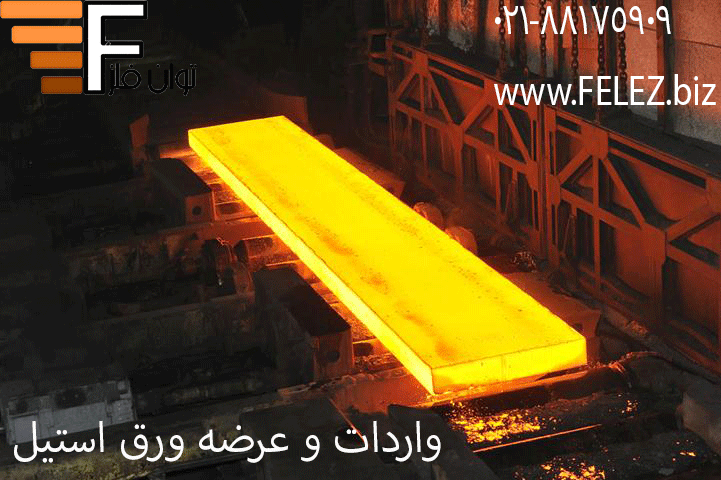
- 20/11/1399 17/8/1401
جهت خرید ورق استیل بصورت ورق ارجینال یا کویل استیل می توانید از طریق شماره تماس : 02188175909 با کارشناسان بخش فروش توان فلز تماس بگیرید.
فهرست موضوعات
عملیات حرارتی ورق استیل
مقدمه
استنلس استیل ها بر مبنای نوع رده آلیاژی (آستنیتی، فریتی، مارتنزیتی، دوپلکس ) و نوع کاربرد تحت عملیات حرارتی قرار می گیرند. فرایند عملیات حرارتی این فولادها شامل تنش زدایی، سخت کاری و آنیل است که منجر به بهبود استحکام، داکتیلیته و مقاومت به خوردگی می شود. همچنین با انجام عملیات حرارتی مقاومت به سایش و مقاومت در برابر فشارهای مکانیکی حین فرایند های فرم دهی و شکل دهی که جهت تبدیل به محصولات نهایی انجام می شود، افزایش می یابد. عملیات حرارتی فولاد های زنگ نزن عمدتا تحت شرایط کنترل شده صورت می گیرد تا از کربن دهی ( کربوره شدن )، دفع کربن و پوسته پوسته شدن سطح جلوگیری شود.
عملیات آنیل
فرایند آنیل یا عملیات محلولی، برای وقوع تبلور مجدد در ورق استیل آستنیتی کارسخت شده و همچنین انحلال کاربید های کروم که در اطراف مناطق کارسخت شده و مرزدانه رسوب زایی کرده اند، انجام می شوند. زیرا رسوب زایی کاربیدها در این مناطق منجر به خوردگی بین دانه ای خواهد شد. همچنین عملیات آنیل منجر به از بین رفتن تنش های پسماند و باقی مانده حاصل از فرایندهای مکانیکی و دندریت های ایجاد شده حین جوشکاری می شود. عملیات آنیل استنلس استیل ها معمولا در درجه حرارت های بالا تر از ۱۰۴۰ درجه سانتی گراد انجام می گیرد، ولی بسته به نوع رده آلیاژی، تحت شرایط کنترل شده و در دمایی پایین تر ۱۰۱۰ درجه سانتی گراد نیز انجام می شود که در این صورت ساختار دانه بندی حاصل ریزدانه خواهد شد. این فرایند به مدت کوتاهی ادامه می یابد، تا مانع از پوسته پوسته شدن سطح و رشد دانه ها جلوگیری شود.
سرمایش پس از عملیات آنیل (کوئنچ)
به منظور غلبه بر عیوب و حساسیت هایی (رسوب زایی کاربیدها) که طی سرمایس آهسته ایجاد می شود، استنلس استیل های آنیل شده تحت سرمایش سریع (کوئنچ) قرار می گیرند.
آنیل پایدار سازی
این نوع از عملیات حرارتی، برای گریدهای 321 و 347 پس از آنیل های معمول انجام میگیرد. کربن موجود در ترکیب شیمیایی این دو فولاد می تواند با تیتانیم در خلال فرایند آنیل ترکیب گردد. با رسوب زایی کربن در قالب کاربید نیوبیوم یا کاربید تیتانیوم، به واسطه حرارت دهی در بازه دمایی ۸۷۰ تا ۹۰۰ درجه سانتی گراد، به مدت ۲ تا ۴ ساعت و همچنین سرمایش سریع، از تشکیل رسوب کاربید کروم جلوگیری می شود. فرایند آنیل پایدارسازی را می توان تحت شرایط خورندگی زیاد ( فاسد شونده) یا در طیف حرارتی 400 تا ۸۷۰ درجه سانتی گراد انجام داد.
تمیزکاری سطحی
سطح ورق استیل آستنیتی میبایست به دقت تمیز گردد، تا بقایای کربنی و روغن (بازمانده روغن از فرایندهای ترمومکانیکی مراحل قبل از عملیات حرارتی)، قبل و بعد عملیات حراراتی از بین روند، چرا که وجود موارد ذکر شده منجر به کربوراسیون (کربن دهی) می گردد و در نتیجه مقاومت در مقابل خوردگی را کاهش می دهد.
فرایند آنیل
تمامی استنلس استیل های فریتی و مارتنزیتی را می توان با حرارت دهی در محدوده دمایی ناحیه فریتی و یا بالاتر از دمای بحرانی در محدوده آستنیتی (آنیل کامل)، آنیل نمود. همچنین می توان عملیات آنیل را در دمایی پایین تر از دمای بحرانی (آنیل زیر دمای بحرانی) در بازه دمایی 760 الی 830 درجه سانتی گراد انجام داد. با اعمال سرمایش (سرد کردن در دمای 25 درجه سانتی گراد) روی نمونه هایی که به مدت یک ساعت به طور کامل و یا زیر دمای بحرانی آنیل شده اند می توان به ساختاری شامل فریت و کاربیدهای کروی دست یافت. معمولا استنلس استیل هایی که پس از آنیل کامل تحت فرایند کار سرد قرار گرفته اند می توانند در مدت زمانی کمتر از 30 دقیقه در زیر دمای بحرانی آنیل شوند.
فولادهای زنگ نزن فریتی معمولا تا قبل از آنیل در محدوده دمایی 760 الی 955 که منجر به تبلور مجدد می شوند به صورت تک فاز باقی می مانند.
کنترل اتمسفر در عملیات حرارتی
کنترل شرایط در خلال فرایند آنیل منجر به کاهش پوسته پوسته شدن سطح می شود. معمولا عملیات آنیل در یک حمام نمکی (منظور از حمام نمکی محیط انجام عملیات حرارتی است) انجام می شود. یکی از فرایندهای آنیل که به عملیات آنیل براق (Bright Annealing) نیز معروف است در شرایط کنترل شده شدیدی انجام می شود. تولیدکنندگان فولادهای زنگ نزن معمولا عملیات آنیل براق Bright Annealing را روی سیم، تیوب ها و کویل های ورق استیل را در فضایی که نیتروژن و هیدروژن است انجام می دهند. محصولاتی که تحت فرایند آنیل براق ایجاد شدند معمولا نماد BA به آن ها اضافه می شوند. سطح براق معمولا یکی از سطوح پایانی در ورق استیل است.
سخت کاری
ورق استیل مارتنزیتی مانند فولادهای کم آلیاژ (فولادهای با عناصر آلیاژی کم) بوسیله تمپر، کونچ و آستنیته کردن سخت می شوند. محدوده دمایی عملیات آستنیته کردن بازه دمایی 980 الی 1010 درجه سانتی گراد است. سختی در اثر کوئنچ کردن از دمای 980 درجه سانتی گراد (دمای آستنیته) ابتدا افزایش می یابد و سپس افت می کند. درجه حرارت بهینه جهت آستنیت نمودن گریدهای مختلف می تواند بر مبنای درجه حرارت عملیات تمپر تعیین شود.
با انجام یک مرحله عملیات پیش گرم در دمای 790درجه سانتی گراد قبل از عملیات آستنیته کردن می توان از ایجاد ترک در مناطقی کم کربن و پر کربن (مناطقی که اختلاف غلظت کربن وجود دارد) جلوگیری نمود.
سرمایش و کوئنچ
استنلس استیل های مارتنزیتی دارای مقادیر بالایی از عناصر آلیاژی هستند، از این رو قابلیت سخت شوندگی بالایی دارند. دستیابی به بالاترین میزان سختی را می توان از طریق سرمایش در هوا از دمای عملیات آستنیته کردن بدست آورد. افزایش سختی قطعات بزرگ بوسیله کوئنچ در روغن حاصل می شود. قطعات سخت شده پس از سرمایش در هوا و به ویژه کوئنچ شده در روغن باید بلافاصله تحت عملیات تمپیر قرار گیرند. زیرا این کار از ایجاد ترک جلوگیری به عمل می آورد. گاهی قطعات ساخته شده از استنلس استیل را که قرار است تحت عملیات تمپر قرار گیرند قبل از تپمر شدن در دمای C֯ 75- فریز می شوند. فرایند تمپر استنلس استیل های مارتزیتی معمولا در دمایی بالاتر از 510 درجه سانتی گراد و سرمایش سریع از دمای 400 درجه سانتی گراد به منظور جلوگیری از تردی و شکنندگی انجام می شود.
بعضی از استنلس استیل های پیر سخت شده در مقایسه با فولادهای مارتنزیتی به شرایط کنترلی دقیق تری در عملیات حرارتی نیاز دارند. به عنوان مثال، پیرسازی، سرمایش زیر صفر و عملیات آنیل ممکن است به پیرسختی بوسیله یک عملیات نیمه آستنیتی نیاز داشته باشند. اما استنلس استیل های مارتنزیتی پیرسخت شده تنها به عملیات پیرسازی نیاز دارند.
تنش زدایی (رها سازی تنش)
انجام فرایند های مکانیکی روی مقاطع فولادی منجر به ایجاد تنش در ماده می شود که به این تنش ها، تنش های باقی مانده یا تنش پسماند می گویند. تنش های باقی در مواد به عنوان عیب محسوب می شوند. این تنش ها معمولا در اثر حرارت دهی از بین می روند. عملیات تنش زدایی یا رها سازی تنش معمولا در دمایی پایین تر از 400 درجه سانتی گراد انجام می شود که در این دما منجر به کاهش میزان متوسطی از تنش های باقی در ماده می شود. اگر عملیات تنش زدایی در محدوده دمایی 425 الی 925 انجام شود میزان بالایی از تنش های باقی مانده در قطعه کاهش می باید که در غیر اینصورت امکان ناپایداری ابعادی و ترک خوردگی تنشی وجود دارد. معمولا تنش زدایی در دمای 870 درجه سانتی گراد به مدت یک ساعت 85 درصد از تنش های باقی مانده در قطعه را از بین می برد. اما این نکته را نیز باید یادآور شد که این طیف حرارت دهی می تواند باعث رسوب کاربیدها در مرز دانه ها شود. در این صورت احتمال خوردگی بین دانه ای افزایش می یابد. به عنوان مثال ورق استیل 304 در محدوده دمایی 425 الی 860 و ورق استیل 310 نسوز در طیف حراراتی 550 الی 800 درجه سانتی گراد در معرض رسوب زایی کاربیدها قرار دارند. هرچه قدر میزان کربن کمتر باشد رسوب زایی کاربیدها در فولادهای زنگ نزن کاهش می یابد. بنابراین احتمال وقوع خوردگی بین دانه ای در فولادهای زنگ نزن با کربن پایین تر، کمتر است. مثلا ورق استیل L 304 در مقایسه با گریدهای 304 و H 304 کمتر در رسوب زایی کاربیدها و خوردگی بین دانه ای در این بازه دمایی قرار دارند.
سیکل عملیات محلولی (عملیات حرارتی محلولی یا آنیل انحلالی) فولادهای زنگ نزن شامل حرارت دهی در دمایی حدود ۱۰۸۰ درجه سانتی گرا و سرمایش سریع است که تنش های باقی مانده در ماده را از بین می برد. با این وجود، این عملیات برای اغلب تجهیزات پیچیده یا بزرگ کاربرد ندارد.
تنش زدایی در دمای پایین
کارسرد یا عملیات مکانیکی در دمای محیط که در ورق استیل منجر به افزایش استحکام می شود، میزان تنش پسماند را نیز افزایش می دهد. بنابراین پس از اعمال کار سرد نیاز به عملیات تنش زدایی وجود دارد. اگر مقاومت به خوردگی دانه ای مهم نباشد عملیات تنش زدایی می تواند در محدوده دمایی 345 الی 425 درجه سانتی گراد انجام شود. عمل تنش زدایی درجه حرارت های بالاتر از این بازه دمایی (345 الی 425) منجر به افت استحکام شده، و برای تنش زدایی محصولات کار سرد شده توصیه نمی گردد.
عملیات حرارتی پس از جوشکاری
محصولات جوشکاری شده از جنس استنلس استیل معمولا در دمایی پایین تر از دمای عملیات آنیل تحت حرارت دهی (تنش زدایی) قرار می گیرند تا میزان تنش های باقی مانده کاهش یابد در حالی که عملیات آنیل پس از جوشکاری امکان پذیر نمی باشد. تنش زدایی معمولا روی قطعات بزرگ یا قطعات با شکل پیچیده که تحت جوشکاری قرار می گیرند و یا زمانی که دو آلیاژ متفاوت مثلا یک فولاد کم آلیاژ به فولاد ضد زنگ جوش داده شده باشد انجام می شود.
سخت کاری سطحی
تنها برخی از انواع روشهای سخت شدن سطحی را می توان روی ورق استیل (استنلس استیل ها) انجام داد. در اغلب موارد، سخت نمودن سطحی فولادهای آلیاژی با عناصر کم (کم آلیاژ) و کربنی به استحاله مارتنزیتی بستگی دارد، چنان که سختی حاصله به میزان (محتوا) کربن بستگی پیدا می کند. با این وجود، این روش سختی کاری به میزان گسترده ای به کار نمیرود، چرا که میزان کربن در گریدهای استنلس استیل مارتنزیتی متغیر است.
نیتروژن دهی
سختی سطحی ورق استیل آستنیتی را می توان با فرایند نیتروژن دهی افزایش داد. این فرایند کاربرد بسیار محدودی دارد، چرا که مغز مقاطع استنلس استیل نرم بوده و از استحکام پایینی برای کاربردهای سنگین برخوردار می باشد. محدودیت عمده دیگر این است که فولاد نیتروژن داده شده مقاومت کمتری در مقایسه با فولاد زنگ نزن اصلی در مقابل خوردگی دارد.
رسوب دهی بخار فیزیکی (انباشت بخار فیزیکی)
رسوب دهی بخار (PVD) فیزیکی امکان ایجاد لایه های نازک و سخت را بر روی بسیاری از مواد از جمله ورق استیل را می دهد. تیتانیوم نیترید پرکاربردترین پوشش موجود در این زمینه می باشد که رنگ طلایی و ظاهری زیبا دارد. به دلیل شکل ظاهری، این روکش با عنوان سطح آینه ای (No.8) برای تولید پنل های معماری به کار می رود.