ورق استیل در تولید توربین های بخار
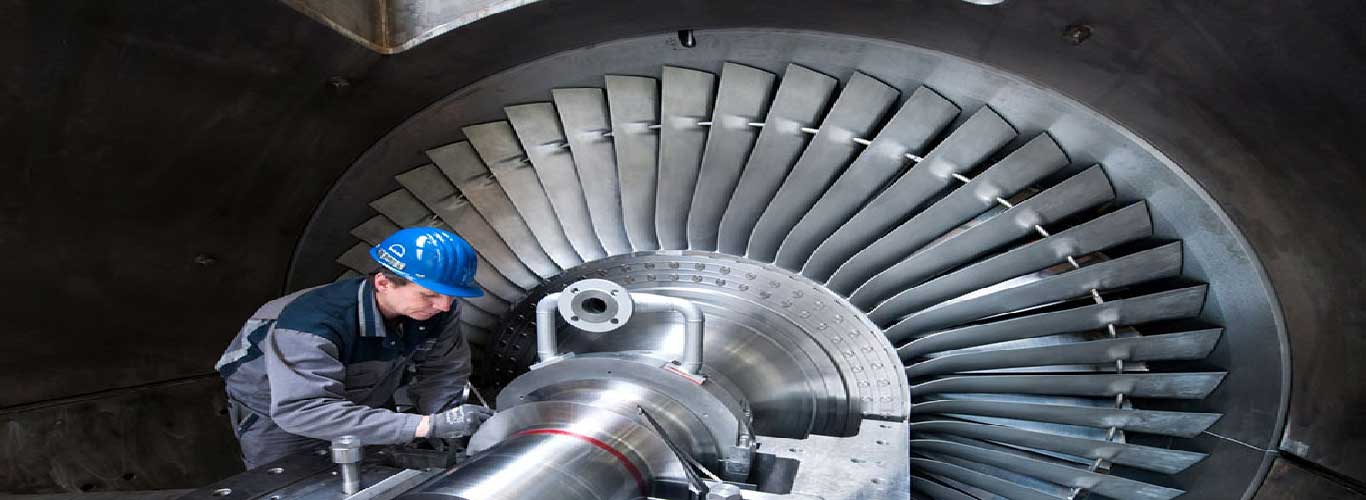
- 4/11/1400 17/8/1401
فهرست موضوعات
مقدمه
از زمان تولید اوّلین توربین بخار زمینی در کشور ژاپن با ظرفیت 500 کیلووات در سال 1908، توربینهای بخار تا به امروز پیشرفت بسیاری داشتهاند و ظرفیّت آنها به بیش از 360 گیگاوات رسیده است. دلیل اصلی استفاده گسترده از توربینهای بخار این است که طی سالیان متمادی این توربینها سابقه اثبات شدهای در تامین برق پایدار با موفقیت رضایتبخش از خود به اثبات رساندهاند. سایر عوامل مهمّی که کاربرد آنها را افزایش داده است، عبارت از این واقعیت میباشد که شرایط تولید بخار با پیشرفت تکنولوژی بهبود یافته است و توربینهای بخار به تکامل خود ادامه دادهاند و با به کارگیری سریع آخرین فناوریهای تجزیه و تحلیل در طراحی خود و به کارگیری فناوریهای به روز برای راندمان و قابلیت اطمینان بیشتر به تقاضای انرژی الکتریکی پاسخ قابل قبولی میدهند. استفاده از ورق استیل بگیر به عنوان مواد مورد استفاده در تجهیزات جدید توربینهای بخار نظیر ورق استیل 410 در افزایش راندمان توربینهای جدید نقش به سزایی داشته است. قیمت ورق استیل بگیر بهگونهای است که استفاده از آن را توجیهپذیر و مورد توجّه طراحان قرار داده است.
یکی از نگرانیهای تولیدکنندگان توربینهای بخار موضوع زیست محیطی میباشد که در سالهای اخیر تقاضای فزایندهای برای افزایش ظرفیت خروجی توربینها همزمان با بهبود کارایی آنها با استفاده از انواع ورق استیل بگیر نظیر ورق استیل 410 داشته است. سازگاری و قیمت ورق استیل بگیر کیفیّتی را در اختیار طرّاحان قرار داده است که بتوانند طیف وسیعی از انواع توربینهای بخار شامل نیروگاههای حرارتی با سوخت زغال سنگ تحت فشار زیر بحرانی تا نیروگاههای فعّال تحت فشار فوق بحرانی و فشار فوق العاده بحرانی را تولید نمایند. همین خاصیت موجب گردیده است که تنوع وسیعی از توربینها در دسترس دولتها و شرکتهای تولید برق قرار بگیرد.
ساختار توربین بخار
تیغههای توربینهای بخار به عنوان قلب آن محسوب میشوند، زیرا آنها عناصر اصلی در تبدیل انرژی حرارتی به انرژی جنبشی هستند. کارایی و قابلیت اطمینان یک توربین به طراحی مناسب پرهها بستگی دارد. بنابراین برای همه مهندسین توربین بخار لازم است که یک دید کلی از اهمیّت و جنبههای طراحی اوّلیه پرههای توربین بخار داشته باشند. طراحی تیغه یک علم چند رشتهای است که شامل رشتههای ترمودینامیک، آیرودینامیک، مکانیک و علم مواد است. بنابراین توسعه کامل یک تیغه جدید تنها زمانی امکانپذیر است که متخصّصان همه این زمینهها به عنوان یک تیم گرد هم آیند. تقریباً تمام پرههای مورد استفاده در توربینهای بخار مکانیکی مدرن از نوع کشیده شده یا آسیاب شده است. تیغههای کشیده شده از مواد به شکل ایرفویل اکسترود شده و ماشینکاری می شوند. تیغههای آسیاب شده نیز از یک قطعه مستطیل شکل از استوک میله ماشینکاری میگردد. بازده توربین به پارامترهای زیر بستگی دارد:
- زاویه ورودی و خروجی تیغه
- مواد تیغه
- مشخصات تیغه
- تکمیل سطح تیغه
مهمترین جنبه قابلیت اطمینان توربین بخار بر روی طراحی بدنه آن متمرکز است. از آنجایی که بدنه و تیغههای دوّار در حین کار در معرض نیروهای بخار ناپایدار قرار میگیرند، پدیده تشدید ارتعاش باید در نظر گرفته شود. رزونانس زمانی رخ میدهد که یک فرکانس تحریک کننده با فرکانس طبیعی سیستم منطبق باشد. در شرایط تشدید، دامنه ارتعاش در درجه اول به مقدار محرّک و میرایی موجود در سیستم مربوط میشود. قابلیت اطمینان بالای محفظه مستلزم طرحهایی با حداقل لرزش رزونانس است. فرآیند طراحی با محاسبه دقیق فرکانسهای طبیعی محفظه در حالتهای مماسی، محوری، پیچشی و پیچیده آغاز میشود که با دادههای آزمایشی تأیید میشوند. علاوه بر این، شکلهای آیرودینامیکی بهبود یافته نازل و فاصلههای محوری دقیق باعث کاهش لرزش محفظه میگردد. همچنین پوشش محفظه در برخی از بخشهای توربین برای کاهش ارتعاشات القا شده استفاده میشود. این شیوههای طراحی، همراه با تکنیکهای پیشرفته ساخت دقیق، اطمینان لازم محفظه را تضمین میکند.
عوامل فنی درطراحی توربین بخار
همانگونه که گفته شد طراحی تیغههای توربین بخار یکی از مهمترین بخشهای ساخت آن بوده و طراحی تیغهای کارآمد و قابل اعتماد است که شرایط زیر را برآورده نماید:
1- مواد تیغه باید دارای استحکام تسلیم کافی برای مقاومت در برابر تغییر شکل پلاستیکی باشد و بتواند برای حفظ در دماهای بالا به مقدار قابل قبولی این خاصیت را حفظ نماید.
2- مواد تیغه باید به راحتی قابلیت تغییرشکل، اتصال و ساخت را داشته باشند. این خاصیت یکی از نقاط ضعف آلیاژهای تیتانیوم است، زیرا به راحتی جوش داده نمی شوند و تولید آنها گران است.
3- مواد تیغه باید مدول الاستیک متوسطی از خود نشان دهند تا اولاً تیغه بیش از حد تغییر شکل ندهد و ثانیاً به طور ناگهانی تحت تنشهای عملیاتی معمولی دچار شکست نشود.
4- ترجیحاً مواد تیغه باید دارای چگالی کم باشند تا نیروهای گریز از مرکز کاهش یابد و بنابراین فشارهای گریز از مرکز بر روی تیغهها به حداقل ممکن برسد.
5- تیغهها باید در برابر خوردگی مقاوم باشند. به نحوی که حتی در حضور محلولهای یونی تهاجمی تشکیل شده توسط ناخالصیهای موجود در بخار مقاومت کافی داشته باشند.
6- تیغهها باید به گونهای ساخته شوند که شروع ترکها در طول دوره به حداقل برسد.
سیدرحیم کیاحسینی